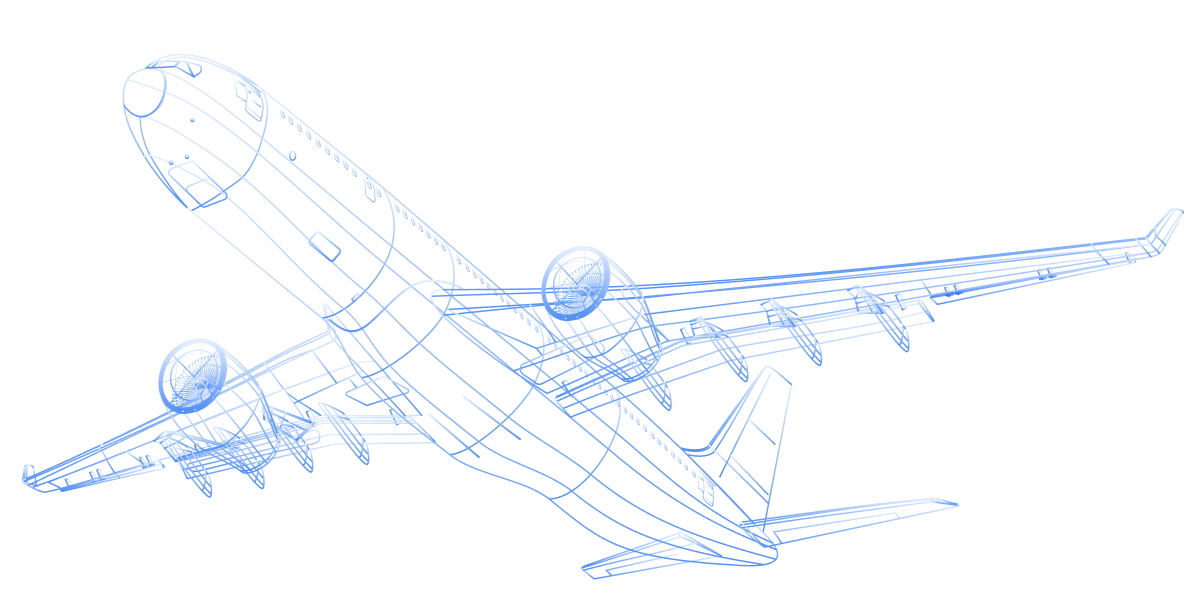
Join the team
View OpeningsListings
Quality Control Manager
Responsibilities:
The Quality Control Manager is expected to lead the Quality team for the repair station in the execution of the below stated responsibilities.
- Coordinate and distribute revisions to all controlled manuals.
- Coordinate FAA inspections as delineated by RSM & QCM.
- Respond to any request for an inspection of the company’s certificate.
- Ensure that work accomplished outside the repair station’s fixed location is performed in accordance with this manual. Determine the final disposition of articles failing to meet the incoming inspection review.
- Ensure appropriate calibrations and checks are made on the tools and equipment used by this repair station.
- Ensure records of all calibrations and checks are kept current, and the calibrations are performed in accordance with the standards and procedures described in the Quality Manual.
- Audit all maintenance function contractors before use and maintain the results of those audits.
- Establish and maintain this repair station employment and training records.
- Perform the repair station’s “self-evaluation” to determine whether it has the housing, facilities, equipment, material, data, and trained personnel to add an article to its Capability List.
- Ensure all technical data is current.
- Gather the necessary documents and reports for final review. These documents shall include, but are not limited to, work order packages, purchase orders, training records, and calibration records.
- Responsible for maintenance of the quality system and all record keeping.
- Ensure that procedures are in place to obtain information with respect to the pertinent sections of Title 14 Code of Federal Regulations and Airworthiness Directives (AD).
- Ensure that procedures for shelf life are adequate and maintained current.
- Maintain all maintenance corrective action and training policy and procedures as delineated in the QC Manual
- At the direction of the AM, coordinate FAA inspections as delineated in this manual.
- Ensure all incoming, hidden damage, preliminary, in-process, and final inspections are performed in accordance with the policy and procedures as delineated in the QC Manual.
- Submit reports of serious defectors recurring un-airworthy conditions in accordance with the policy and procedures as delineated in the QC Manual.
- Ensure that all maintenance and inspection forms used by the repair station are complete prior to releasing articles for return to service. This is to include the FAA Form 8130-3.
- Ensure that all maintenance performed under the repair station certificate is done so in accordance current FAA regulations, manufacturer’s specifications or any other data acceptable to the FAA.
- Review and disposition all warranty returns, and track warranty return rates. Evaluate warranty return history and conduct root cause analysis and corrective actions as appropriate.
- Ensure that reports of serious defects or recurring non-airworthy conditions are submitted in accordance with the policy and procedures delineated in the QC Manual.
- Maintain the Technical Data, scrap program and procedures as delineated in the QC Manual.
- Ensure that all internal audits are performed and documented pursuant to the policies and procedures set forth in this QC Manual.
- Ensure that all corrective, preventive, and root cause actions for all audits internal and customer are taken, documented, and communicated to upper management and AM.
- Establish liaison with air carriers with respect to the applicable sections of Title 14 Code of Federal Regulations when work for air carrier is to be performed.
- Ensure that personnel follow, are trained and informed of the procedures for inspecting articles for maintenance and material.
- Perform other duties and / or projects as assigned.
Qualifications: Priorto being assigned as the Manager of Quality, or any person assignedtechnical supervisory responsibilities and being listed on the repair stationroster, this repair station shall determine that the individual:
· Is appropriately certificated under FAR Part 65.
· Understands the FARs, Airworthiness Directives, methods,techniques, and practices contained in the applicable manufacturers’maintenance and alteration documents and/other data acceptable to or approvedby the FAA used by the repair station.
· Has the appropriate experience, evidenced by employmenthistory, training, certification or practical tests to perform in thesupervisory position assigned.
· Once the above information has been ascertained anddocumented in the appropriate employment file, the person shall be listed onthe repair station roster.
· Bachelor’s degree (B.A.) or equivalent or four to sixyears related experience and/or training.
- Ability to solve problems under time constraints.
- Strong organizational, problem-solving, and analytical skills; able to manage priorities and workflow.
- Versatility, flexibility, and a willingness to work within constantly changing priorities with enthusiasm.
- Must have strong analytical skills and be versatile as well as have healthy experience of collection and analysis of complex data, both narrative and statistical.
- Excellent communication/interpersonal skills to build effective working relationships.
- Ability to work independently and within a team.
- Ability to handle stress and demonstrate strong problem-solving ability.
- The candidate should be active, self-motivated, a quick learner, and innovative.
- Ability to multi-task and in a fast paced, changing environment.
- Ability to prioritize assigned work, organization skills.
· Reportsto: Director of Operations